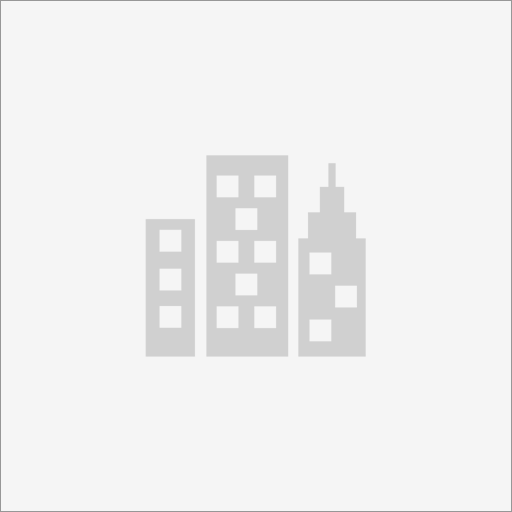
Unilever Canada Inc
The Maintenance Lead role is critical to the development of our factories to World Class, which means zero defects, zero waste and zero losses. The Maintenance Lead role will focus on elimination of breakdowns and maintenance of basic conditions through use of Focused Improvement and Quality improvement methods including implementation of countermeasures that simplify processes, utilize predictive / preventative maintenance effectively and introduce increased automation and controls.
Key Skills and Competencies:
Consumer & Customer Focus. Building world class factories will eliminate losses and ensure that we do not pass on the cost of inefficiencies to our customers and consumers.
Bias for Action. By providing consistent and near real time information, decisions can be taken quickly which leverage our resources.
Building Talent & Teams. Our vision is to move to semi-autonomous teams and we require Maintenance Lead with a passion for achieving results through great teamwork, an ability to teach new tools and methodologies and ensuring that you and your colleagues are fully aligned, and drawing on one another’s strengths.
Accountability & Responsibility. Taking responsibility for building your team’s performance and sharing your best interventions to help support other lines’ in their improvements.
Growth Mindset. By building world class factories, we will become more competitive in the marketplace and set the standards to which others aspire.
Apply the full set of UMS methods and tools to identify root causes, define countermeasures and validate their effectiveness; Establish standards to support line operators and mechanics sustain new basic conditions.
Process and Organizational Design. Leverage technical knowledge and a systems approach to ensure factory lines and processes are optimally resourced.
Analytical capability. Collect and analyze complex data to penetrate problems’ phenomena and understand root causes.
Key Deliverables For Maintenance Lead :
Eliminate Loss according to the UMS prioritization process using PM, FI and QC pillar tools and methodologies.
Implement preventative, predictive maintenance and design / automation improvements to maintain basic conditions and increase MTBF
Train maintenance crews on technical standards and sustainability of basic conditions (Stability sustainability).
Identify and extend good practice to other lines.
Key Performance Indicators (as driven by Cost Deployment Analysis):
Breakdowns (PM Loss), MTBF, Maintenance Cost
Benefit/Cost Ratio
Spare parts standards, define critical parts and maintain.
Qualifications For Maintenance Lead:
- Strong troubleshooting skills;
- Able to visualize clearly what the ideal production system is;
- Able to clearly understand operating principles and establish correct operating standards;
- Able to present findings and rationales clearly so that whole factory team can understand;
- Able to make logical decisions based on data;
- Possess challenging and pioneering spirit.
- Post Graduate level education; Mechanical, Chemical or Electrical Engineering or similar.
Experience Required:
- Must have 3-5 years of leadership experience in food manufacturing or other industries.
- Experience in automation and controls, control panels- Allen Bradley
- Experience with NFPA 70E electrical safety standard, electrical designs, schematics, Autocad
- Experience with P&IDs, PFDs, HAZOP, FMEA
- Experience in statistics and process control tools.
- Experience in AM, PM, Quality and FI tools and processes.
- Confident in applying problem solving tools (5W1H, 4M, 5WHY etc.)